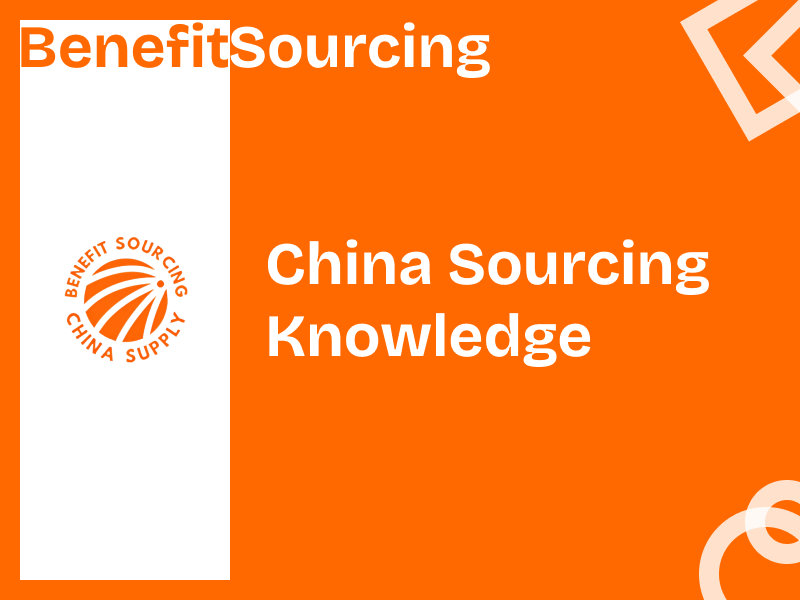
Step 1: Define Your Quality Standards
Start by clarifying what “quality” means for your specific product. Research industry - specific standards (e.g., ISO certifications, CE marks, ASTM International guidelines) and align your checklist with these benchmarks. For example, electronics might require safety certifications like RoHS compliance, while textiles may need OEKO - TEX® certification. Collaborate with suppliers to ensure they understand these requirements and can meet them consistently.
Step 2: Break Down the Product Specifications
Create a detailed list of product attributes to verify:
- Physical dimensions: Measure length, width, weight, and tolerances.
- Material composition: Verify fabrics, metals, or plastics against agreed specifications.
- Functional performance: Test battery life, water resistance, or load - bearing capacity.
- Aesthetics: Check color accuracy, stitching quality, surface finishes, and logo placement.
Request product samples early in the process to confirm these details before mass production.
Step 3: Inspect Raw Materials
Quality assurance begins at the source. Ask suppliers to:
- Provide material certificates (e.g., metal alloy grades, fabric composition).
- Share test reports from accredited labs for critical components like lithium batteries or food - contact materials.
- Use trackable batch numbers for raw materials to simplify traceability if defects arise later.
Step 4: Monitor Production Processes
Implement in - process checks to catch issues early:
- Critical control points: Identify high - risk stages (e.g., welding in machinery, dyeing fabrics) and conduct spot checks.
- Equipment calibration: Ensure machinery is maintained and calibrated weekly / monthly.
- Workmanship standards: Audit assembly lines for proper techniques, like consistent solder joints or stitch density.
For remote monitoring, request time - stamped photos / videos of production milestones or hire third - party inspectors for unannounced visits.
Step 5: Conduct Pre - Shipment Inspections
Follow the AQL (Acceptable Quality Level) sampling method:
- General Inspection Level II: Commonly used for balanced rigor.
- Defect classification:
- Critical: Issues causing safety hazards (e.g., exposed wires, sharp edges) – 0% tolerance.
- Major: Problems affecting functionality (e.g., broken zippers, incorrect voltage) – allow ≤2.5% defects.
- Minor: Cosmetic flaws (e.g., slight color variations, minor scratches) – allow ≤4.0% defects.
Document findings with photos and videos, specifying batch numbers for defective units.
Step 6: Verify Packaging and Labeling
Ensure packaging protects products during transit and complies with destination regulations:
- Shipping tests: Conduct drop tests for fragile items (e.g., simulate 3 - foot drops onto concrete).
- Label accuracy: Check for correct SKUs, country of origin, multilingual warnings, and barcode readability.
- Customs compliance: Include harmonized system (HS) codes, FDA / FCC marks if applicable, and safety manuals.
Step 7: Review Documentation
Collect and cross - verify all paperwork:
- Quality control reports: Signed by factory QC managers.
- Compliance certificates: Like children’s product CPSIA reports for the US market.
- Shipping documents: Commercial invoices with INCOTERMS®, packing lists, and bill of lading.
Step 8: Establish a Feedback Loop
Build a system for continuous improvement:
- Supplier scorecards: Rate suppliers quarterly on defect rates, on - time delivery, and responsiveness.
- Customer returns analysis: Categorize return reasons (e.g., 30% due to sizing issues, 15% from packaging damage) and update your checklist accordingly.
- Regular audits: Revisit your QA checklist every 6 months to adapt to new regulations or market trends.
Pro Tip for Small Businesses
If hiring third - party inspectors exceeds your budget, use a phased approach:
- Start with self - inspection guides (checklists with photo examples) for suppliers to complete.
- For high - value orders, split inspection costs with other buyers through group purchasing alliances.
- Gradually invest in inspection tools like USB charge testers, torque wrenches, or color - matching light booths as your business scales.
By integrating these steps, you’ll minimize risks of defective shipments, build trustworthy supplier relationships, and protect your brand reputation in competitive markets.