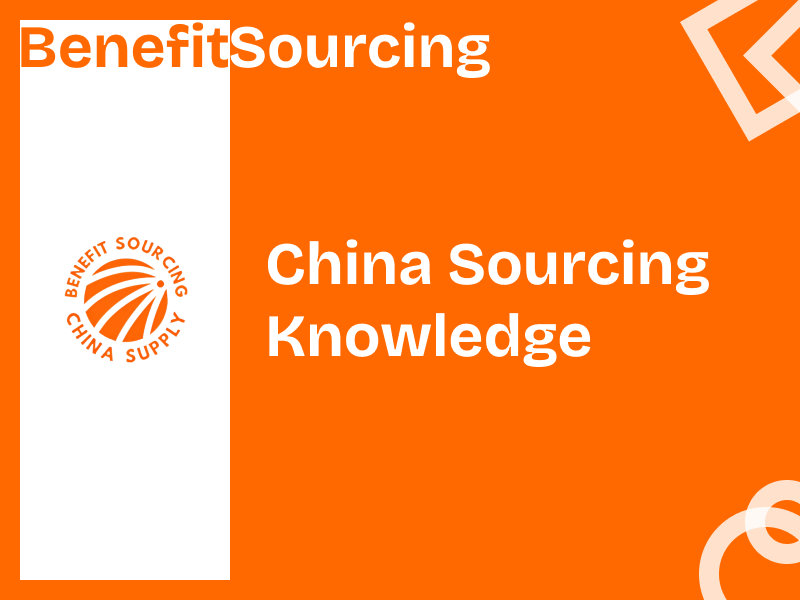
Understanding the Basics
On-site inspections and factory audits are critical steps in ensuring product quality and ethical manufacturing practices when sourcing from China. While often used interchangeably, these processes serve distinct purposes:
- Inspections focus on verifying product quality, specifications, and compliance with order requirements at specific production stages.
- Audits evaluate a factory’s overall capabilities, management systems, and sustainability practices.
For small - volume buyers, combining both approaches maximizes value while minimizing costs.
Preparing for the Visit
- Define Your Objectives
- Determine whether you need a pre - production inspection (to verify raw materials), during - production check (to monitor assembly), or final random inspection (to assess finished goods).
- For audits, decide between capability audits (production capacity), social compliance audits (labor practices), or quality management system audits (ISO 9001 standards).
- Create a Checklist
- Include measurable criteria: defect tolerance levels (e.g., ≤3% for minor defects), production timelines, and safety protocols.
- Download free templates from reputable industry associations to save time.
- Schedule Strategically
- Coordinate with factories 2 - 3 weeks in advance.
- Avoid Chinese public holidays like Lunar New Year (January/February) or National Day (October).
Conducting the Inspection/Audit
Sample Workflow for a Hybrid Approach (Inspection + Basic Audit):
Day 1: Facility Assessment
- Verify business licenses and export certifications.
- Tour production areas: Check machinery maintenance logs, workflow efficiency, and safety equipment availability.
- Interview workers (via translator if needed): Ask about working hours, overtime pay, and training frequency.
Day 2: Product Verification
- Randomly select samples from finished goods (AQL 2.5 is common for consumer products).
- Test key attributes: dimensions, functionality, packaging accuracy.
- Compare results against your provided specifications sheet.
Day 3: Documentation Review
- Examine quality control records from the past 6 months.
- Trace raw material purchases to certified suppliers.
- Review corrective action reports for recurring issues.
Common Red Flags to Watch For
- “Golden Samples” Trap: Factories sometimes prepare perfect samples while mass - produced items differ. Always inspect randomly selected units from bulk batches.
- Double Bookkeeping: Some facilities maintain separate financial records for audits. Cross - check production logs with electricity bills or raw material consumption data.
- Subcontracting Risks: Unauthorized outsourcing is common. Ask to see all production units and verify machinery capacity matches order volume.
Post - Visit Follow - Up
- Analyze Findings
- Use scoring systems: Rate factories on a 100 - point scale (e.g., 80+ = approved, 60 - 79 = conditional approval).
- Flag critical issues like child labor or safety violations for immediate action.
- Negotiate Improvements
- Create a corrective action plan (CAP) with clear deadlines. Example: “Upgrade welding safety gear within 30 days.”
- Offer incentives: Promise larger orders for factories that consistently meet standards.
- Monitor Continuously
- For approved suppliers, conduct annual audits and inspect 10 - 20% of shipments.
- Use video call spot - checks between physical visits to reduce travel costs.
Cost - Effective Alternatives for Small Businesses
- Remote Audits: Many Chinese factories now offer live video tours via WhatsApp or Zoom. While less comprehensive, this works well for micro - businesses testing new suppliers.
- Third - Party Services: Hire local inspection companies for $300 - $500 per visit—far cheaper than international travel.
- Group Sourcing: Partner with non - competing businesses to share audit costs through B2B platforms or e - commerce communities.
Navigating Language Barriers
- Use translation apps like Google Translate or WeChat’s built - in translator for basic communication.
- Prepare key questions in simple English and Chinese:
- “Can I see your quality control records?” → 请给我看看质量控制记录。
- “What is your defect repair process?” → 你们如何处理不合格产品?
- Hire bilingual freelancers on Upwork or Fiverr for $15 - $30/hour to accompany virtual inspections.
Special Considerations for Small Orders
- Sample Validation: For orders under 500 units, pay for 3 - 5 pre - shipment samples to test before full payment.
- Flexible Payment Terms: Use 30% deposit + 70% balance after inspection to maintain leverage.
- Consolidated Shipping: Partner with logistics aggregators to reduce per - unit freight costs for small batches