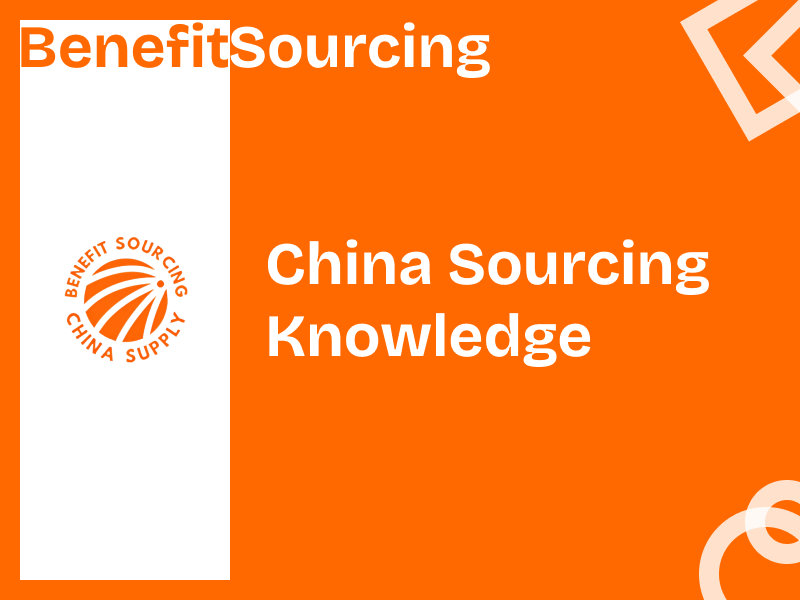
Why Third - Party Quality Verification Matters
For small - to - medium international buyers sourcing products from China, quality control is often the biggest hurdle. While suppliers may provide self - conducted inspections or certifications, conflicts of interest and inconsistent standards frequently lead to defective shipments. Third - party quality verification acts as an independent checkpoint – 42% of cross - border e - commerce disputes stem from product quality issues, according to a 2023 Global Trade Compliance Report.
When to Invest in Third - Party Verification
- New Supplier Relationships
- First - time orders carry the highest risk. A 2022 survey by Trade Assurance International revealed that 68% of quality issues occur during initial transactions with unfamiliar suppliers.
- Verify: Production capabilities, material compliance, and workforce competency
- High - Value or Complex Products
- Prioritize verification for electronics, machinery, or items requiring precise specifications
- Example: A German auto parts retailer reduced return rates by 31% after implementing mandatory third - party component testing
- Regulated Industries
- Essential for products falling under:
- Food safety standards (FDA, EU 178/2002)
- Children’s product safety (CPSIA, EN 71)
- Medical device regulations (ISO 13485)
- Customized Orders
- 55% of customization - related disputes involve mismatched expectations (Source: Global Sourcing Association)
- Conduct pre - production sample validation and mid - production checks
- Small Batch Purchases
- Low - volume buyers (under $20,000 orders) often receive less supplier attention
- Third - party verification ensures equal quality standards regardless of order size
Choosing the Right Verification Partner
| Key Selection Criteria | |
---|
Accreditation | ISO/IEC 17020 or 17025 certification | Non - negotiable for credible inspectors |
Industry Specialization | Look for sector - specific expertise | Electronics inspectors ≠ textile experts |
Geographic Coverage | Local inspectors in supplier’s region | Critical for factory audits |
Reporting Transparency | Real - time digital reports with photo/video evidence | Avoid PDF - only formats |
Cost Structure | Clear per - service pricing | Beware hidden travel/retest fees |
Implementation Steps for Buyers
- Define Quality Benchmarks
- Create a detailed inspection checklist aligned with:
- Product specifications
- Target market regulations
- Packaging/shipping requirements
- Coordinate Timing
- Leverage Technology
- Tools to integrate:
- Blockchain - enabled quality documentation (e.g., IBM TradeLens)
- AI - powered defect detection systems
- IoT temperature/humidity sensors for sensitive goods
- Manage Costs Effectively
| Cost - Saving Strategies | |
---|
Group inspections | Combine multiple small orders | 15 - 20% fee reduction |
Remote auditing | Use AR/video streaming | Cuts travel expenses by 40% |
Supplier incentives | Tie verification costs to long - term contracts | Shared cost models |
Common Verification Mistakes to Avoid
- Over - testing
Testing every parameter increases costs without proportional risk reduction. Focus on critical - to - quality (CTQ) elements.
- Cultural Miscommunication
A UK furniture importer lost $18,000 by assuming “wood grade A” meant the same thing to their Chinese supplier. Always clarify terminology.
- Last - Minute Scheduling
Booking inspections less than 72 hours before shipping often results in rushed, incomplete checks.
- Ignoring Environmental Factors
Humidity/temperature during testing must match destination country conditions – a key oversight for 23% of东南亚 buyers (2023 ASEAN Quality Report).
Emerging Trends in Quality Assurance
- On - Demand Mobile Inspection Teams
Platforms like AsiaInspection now offer Uber - style instant verification bookings in 48 Chinese cities.
- Predictive Quality Analytics
Machine learning models that forecast defect probabilities based on supplier history and production variables.
- Decentralized Verification Networks
Blockchain systems where multiple buyers collectively validate and share supplier quality data.
By integrating third - party verification strategically, small international buyers transform quality assurance from a reactive cost center into a proactive competitive advantage. The key lies in matching verification intensity to risk levels while leveraging modern tools that make professional - grade quality control accessible to businesses of all sizes.