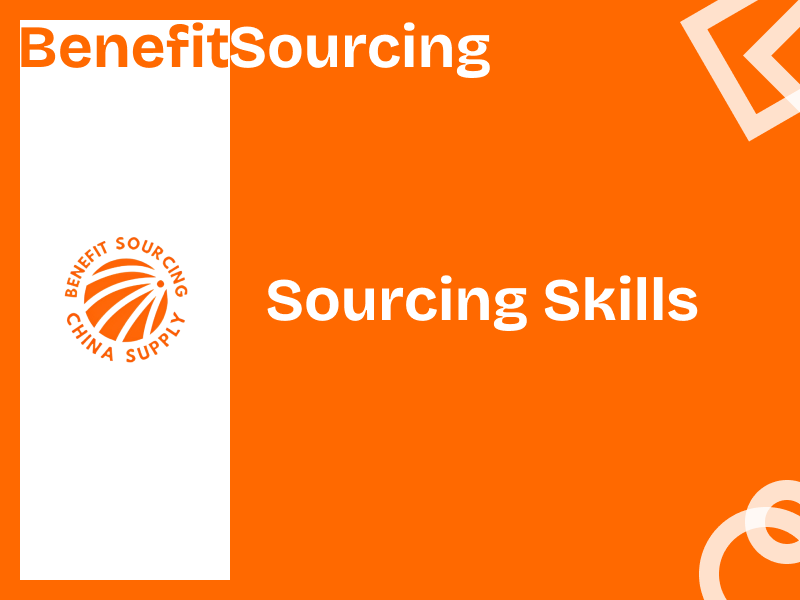
For international small-to-medium businesses (SMBs), individual retailers, and e-commerce sellers sourcing products from China, factory audits are a non-negotiable step to mitigate risks and ensure supply chain stability. Without proper due diligence, quality inconsistencies, production delays, and ethical compliance issues can derail your business. Here’s a practical guide to conducting effective factory audits, even with limited resources:
Why Factory Audits Matter for SMBs
- Avoid Costly Mistakes: A single batch of defective products can damage your reputation and lead to returns or refunds.
- Build Trust: Audits help establish long-term partnerships with reliable suppliers.
- Compliance Assurance: Verify adherence to labor laws, environmental standards, and safety protocols to avoid legal or reputational risks.
Key Areas to Evaluate During a Factory Audit
Focus on these critical aspects to maximize audit efficiency:
-
Factory Credentials and Legitimacy
- Confirm business licenses, export permits, and certifications (e.g., ISO 9001, BSCI).
- Cross-check factory addresses and ownership details via third-party databases like Panjiva or local Chamber of Commerce records.
- Request references from existing clients in your region.
-
Production Capacity and Workflow
- Assess machinery maintenance logs and production line organization.
- Review lead times for sample development and mass production.
- Ask for documentation of past orders similar to your product type and volume.
-
Quality Control Systems
- Inspect QC protocols: How many inspections occur during production? What defect rate is acceptable?
- Verify testing equipment calibration (e.g., torque testers for electronics, colorimeters for textiles).
- Check if the factory uses standardized inspection reports like AQL (Acceptable Quality Level) charts.
-
Ethical and Social Compliance
- Tour worker dormitories and cafeterias (if permitted).
- Review wage records and working hour policies.
- Look for fire safety equipment, emergency exits, and first-aid kits.
-
Communication and Responsiveness
- Test the factory’s English proficiency or availability of translators.
- Evaluate response time to technical queries via email or video calls.
- Confirm designated points of contact for quality issues and logistics.
Cost-Effective Audit Strategies for Small Buyers
When budget or travel constraints exist, try these alternatives:
- Remote Video Audits: Use platforms like Zoom or Microsoft Teams for live facility tours. Request real-time demonstrations of QC checks.
- Third-Party Inspection Services: Hire local inspectors for $200-$500 per audit. Provide them with a customized checklist matching your product requirements.
- Sample Reverse Engineering: Order pre-production samples and disassemble them to check material quality, welding points, or circuitry consistency.
- Supplier Scorecards: Rate factories quarterly using metrics like defect rates, on-time delivery, and communication efficiency.
Red Flags to Watch For
- Overly Perfect Answers: Factories that claim “100% defect-free production” or refuse to share inspection records often hide systemic issues.
- Inconsistent Documentation: Mismatched dates on QC reports or outdated certification copies.
- Unverified “OEM/ODM Experience”: Ask for photographic evidence of custom projects rather than relying on claims.
- Pressure to Skip Deposits: Factories insisting on full upfront payment may lack financial stability.
Post-Audit Actions
- Negotiate a Quality Assurance Agreement (QAA) detailing:
- Penalties for defective shipments (e.g., 5% refund per 1% defect rate)
- Required pre-shipment inspection criteria
- Procedures for dispute resolution
- Start with a small trial order (30%-50% of your target volume) to validate audit findings.
- Schedule surprise follow-up audits during peak production periods to monitor consistency.
Leveraging Technology
- Use blockchain-enabled platforms like VeChain for transparent QC data tracking.
- Implement IoT sensors during production to monitor variables like temperature (for food/products) or assembly line speed.
- Adopt AI-powered tools like Inspectorio to automate audit report analysis and trend prediction.
By integrating these strategies, even resource-limited buyers can systematically reduce supply chain risks. Remember: A rigorous factory audit isn’t about finding the “perfect” supplier—it’s about identifying partners willing to grow with your business through transparent, improvement-focused collaboration.