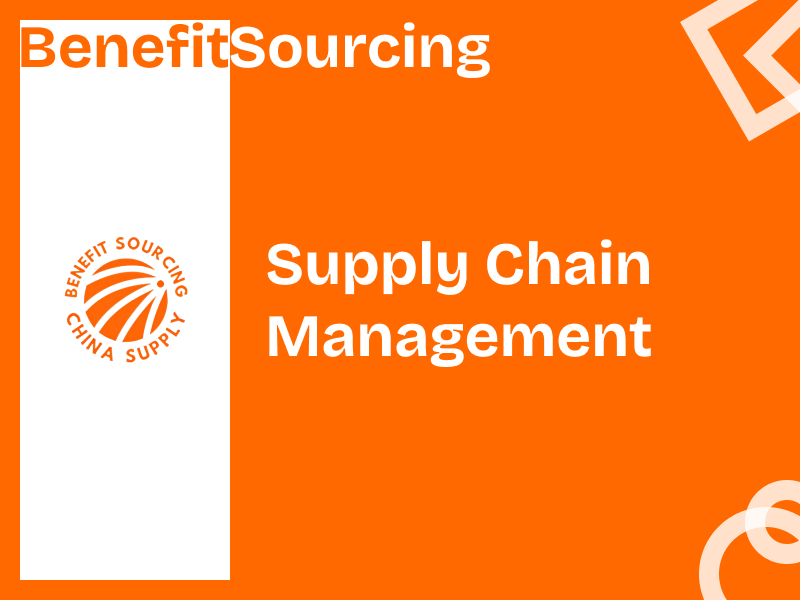
Understanding the Essentials of Supply Chain Management for Small Businesses
For international small business owners, individual retailers, and e-commerce sellers sourcing products from China, mastering supply chain management (SCM) is critical to ensuring smooth operations, cost efficiency, and customer satisfaction. Here’s a practical breakdown of the fundamentals tailored to businesses with limited resources and diverse needs.
1. What Is Supply Chain Management?
SCM involves coordinating the flow of goods, information, and finances from raw material procurement to product delivery. For businesses importing from China, this includes:
- Supplier sourcing: Identifying reliable manufacturers or wholesalers.
- Production oversight: Ensuring quality and timely manufacturing.
- Logistics coordination: Managing transportation, customs, and warehousing.
- Inventory and delivery: Balancing stock levels and meeting customer demand.
A well-optimized supply chain reduces costs, minimizes delays, and enhances scalability—key advantages for businesses with smaller order volumes.
2. Key Challenges and Solutions
Challenge 1: Finding Trustworthy Suppliers
Many foreign buyers struggle to verify suppliers’ credibility due to geographic and language barriers.
- Solutions:
- Use platforms like Alibaba or Global Sources, but prioritize suppliers with “Verified” badges or trade assurance.
- Request samples before bulk orders to assess quality.
- Check business licenses and factory certifications (e.g., ISO, BSCI).
Challenge 2: Navigating Cultural and Communication Gaps
Misunderstandings in negotiations or product specifications can lead to costly errors.
- Solutions:
- Use clear, simple language in communications. Avoid idioms.
- Confirm details in writing (e.g., contracts, purchase orders).
- Hire a local agent or translator if needed.
Challenge 3: Managing Small-Order Logistics
High shipping costs and minimum order quantities (MOQs) often disadvantage smaller buyers.
- Solutions:
- Consolidate shipments with other businesses to share freight costs.
- Opt for sea freight for bulky items (slower but cheaper) or air freight for urgent, lightweight goods.
- Negotiate flexible MOQs by emphasizing long-term partnership potential.
3. Streamlining Processes with Technology
Automation tools help mitigate resource limitations:
- Inventory management software: Tools like TradeGecko or Zoho Inventory track stock levels in real time, preventing overstocking or shortages.
- Supplier relationship management (SRM) systems: Centralize communication and performance data for easier decision-making.
- E-commerce integrations: Link platforms like Shopify or Amazon directly to your supply chain for automated order processing.
For businesses without upfront investment capacity, start with free trials or basic plans.
4. Quality Control Strategies
Protect your brand reputation with these steps:
- Pre-production inspection: Confirm raw materials meet agreed standards.
- During production checks: Visit factories or hire third-party inspectors to monitor progress.
- Pre-shipment inspection: Ensure finished goods align with specifications.
- Random post-delivery checks: Test products periodically after they reach your warehouse.
5. Cost Optimization Tactics
- Bulk purchasing: Partner with other buyers to pool orders and secure volume discounts.
- Negotiate payment terms: Request staggered payments (e.g., 30% deposit, 70% post-inspection) to improve cash flow.
- Compare logistics providers: Use freight marketplaces like Freightos to find competitive rates.
6. Risk Mitigation
- Diversify suppliers: Avoid reliance on a single factory to prevent disruptions.
- Monitor geopolitical factors: Stay updated on trade policies, tariffs, or port strikes that could delay shipments.
- Insurance: Insure high-value shipments against damage or loss.
7. Building Long-Term Supplier Relationships
- Communicate transparently about expectations and feedback.
- Pay invoices promptly to build trust.
- Visit trade fairs like the Canton Fair to meet suppliers face-to-face and explore new partnerships.
8. Sustainability Considerations
Consumers increasingly favor eco-friendly practices. Small steps like:
- Choosing suppliers with ethical labor practices.
- Reducing packaging waste.
- Opting for slower, lower-carbon shipping methods.
Final Tips for Success
- Start with small orders to test suppliers and processes.
- Document every stage of your supply chain for accountability.
- Stay adaptable—regularly review and adjust strategies based on performance data.
By focusing on these fundamentals, even resource-constrained businesses can build efficient, resilient supply chains that support growth and customer loyalty.