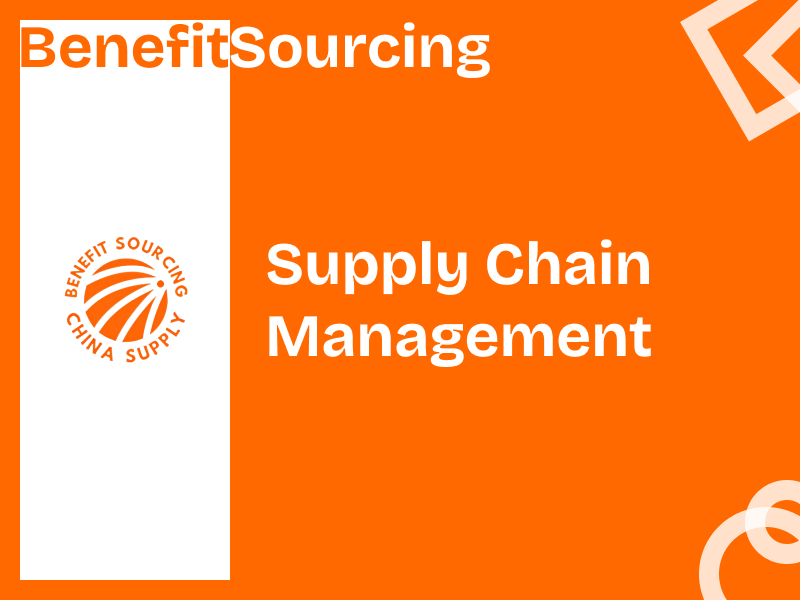
For small and medium-sized businesses, individual retailers, and e-commerce sellers sourcing products from China, implementing robust quality assurance (QA) processes is critical to maintaining customer satisfaction and protecting your brand reputation. Here’s a practical guide to establishing effective QA workflows even with limited resources:
1. Understand Key Quality Parameters
Start by defining clear quality benchmarks for your products:
- Material specifications: Request material safety certificates (e.g., RoHS, REACH) and physical samples for verification
- Performance standards: Identify relevant international certifications (CE, FCC, ISO) for your product category
- Aesthetic requirements: Create visual reference guides with acceptable color tolerances and surface finish standards
2. Leverage Supplier Qualification Processes
Screen Chinese suppliers systematically:
- Verify business licenses through official platforms like the National Enterprise Credit Information Publicity System
- Request past inspection reports from similar clients
- Conduct video audits of production facilities using platforms like Zoom or Teams
- Start with small trial orders (100–500 units) to test consistency
3. Implement Multi-Stage Inspections
Adopt a risk-based approach to quality checks:
- Pre-production: Review raw material certificates and approved prototypes
- During production: Request in-process photos/videos of key manufacturing stages
- Pre-shipment: Use standardized inspection checklists (AQL levels II for visual defects, S-4 for functional testing)
- Post-delivery: Conduct spot checks upon receipt of goods
4. Optimize Inspection Costs
Maximize limited budgets through smart strategies:
- Pool inspection costs with other buyers through sourcing platforms
- Focus on critical-to-quality characteristics rather than 100% checking
- Use mobile inspection apps that allow remote quality verification
- Train local staff in basic QC techniques like measurement verification
5. Address Common Cross-Border Challenges
Mitigate frequent pain points in China sourcing:
- Language barriers: Use translation tools with industry-specific terminology (e.g., KoalaTranslate for manufacturing terms)
- Cultural differences: Learn basic Chinese business etiquette for clearer communication
- Document management: Implement cloud-based systems for organizing certificates and reports
6. Build Continuous Improvement Loops
Establish feedback mechanisms to refine your QA processes:
- Track defect patterns using simple spreadsheets or quality management software
- Conduct quarterly supplier performance reviews
- Share customer return data with manufacturers to drive improvements
- Stay updated on changing regulations in your target market
Practical Tools for Small Buyers:
- Digital inspection platforms: Services like QIMA Online provide pay-as-you-go inspections
- Portable testing devices: Affordable tools like digital calipers and colorimeters for basic checks
- Blockchain verification: Emerging solutions for authenticating certificates and production records
By implementing these structured yet flexible QA processes, you can significantly reduce quality risks while maintaining agility in your China sourcing operations. Start with the highest-risk components of your product line and gradually expand quality controls as your business grows. Remember that consistent communication with suppliers and documented quality records are your best defense against substandard products.