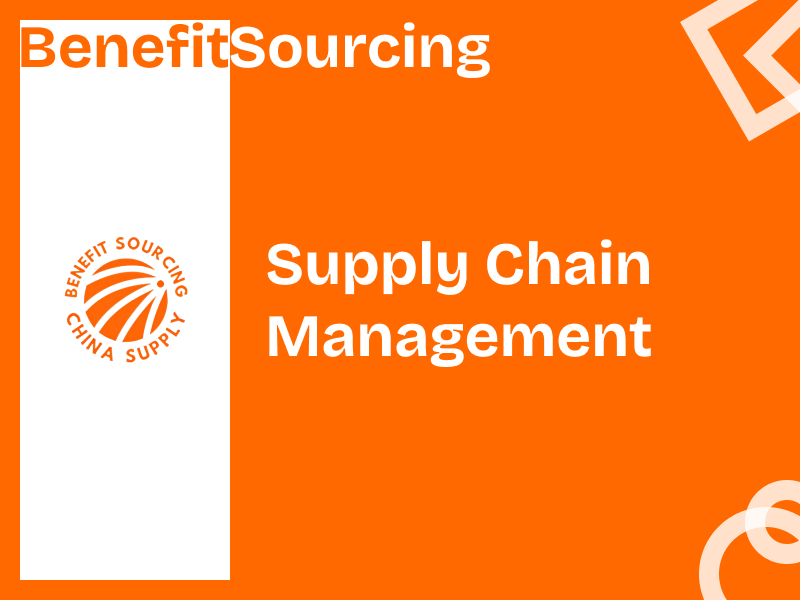
Building a resilient supply chain is crucial for international small businesses sourcing from China. While China’s robust industrial ecosystem offers stability, global disruptions demand proactive emergency preparedness. Here are key strategies tailored for overseas buyers with limited resources:
1. Risk Assessment & Contingency Planning
- Map your entire supply chain to identify single points of failure (e.g., reliance on one factory or shipping route)
- Maintain updated contact lists for all suppliers, logistics partners, and local authorities
- Develop scenario-based response plans for common disruptions:
• Port closures
• Raw material shortages
• Customs delays
• Currency fluctuations
2. Supplier Network Diversification
- Work with multiple manufacturers across different Chinese regions to mitigate regional risks
- Qualify backup suppliers in alternative countries like Vietnam or Mexico
- Split orders between primary and secondary suppliers to maintain relationships
3. Inventory Buffer Management
- Calculate safety stock levels using historical disruption data:
Risk Factor | Recommended Buffer |
---|
High-demand products | 45-60 days |
Customized items | 30-45 days |
Commodity goods | 15-30 days |
- Implement inventory tracking systems with automatic reorder alerts
4. Logistics Redundancy
5. Financial Safeguards
- Establish emergency funds covering:
- 3 months of operational costs
- Unexpected tariff increases
- Emergency air freight expenses
- Negotiate flexible payment terms:
• 30% deposit instead of 50%
• Extended LC periods during crises
6. Digital Infrastructure
- Implement cloud-based tools for:
- Real-time shipment tracking
- Supplier performance monitoring
- Automated customs documentation
- Use blockchain solutions for:
• Product authentication
• Supply chain transparency
7. Cultural & Operational Alignment
- Conduct quarterly video conferences with suppliers to:
- Review quality standards
- Discuss potential bottlenecks
- Align production schedules
- Learn basic Mandarin phrases for critical negotiations
- Understand Chinese holiday schedules impacting production
8. Compliance Readiness
- Maintain updated copies of:
• Product certifications (CE, FCC, RoHS)
• Supplier audit reports
• Shipping insurance policies
- Pre-process customs documentation for fast reshipment
9. Crisis Communication Protocol
10. Continuous Improvement
- Conduct post-crisis reviews to:
- Update risk probability matrix
- Refine contingency plans
- Identify process improvements
- Benchmark against industry standards like ISO 22301 (Business Continuity)
Practical implementation steps for resource-constrained businesses:
- Start with critical SKU analysis (80/20 rule)
- Build supplier scorecards evaluating:
- On-time delivery rate
- Quality consistency
- Communication responsiveness
- Implement weekly supply chain health checks:
- Raw material inventory levels
- Production line status
- Shipping schedule adherence
By integrating these strategies, international buyers can transform their Chinese supply chains from cost centers to competitive advantages. The key lies in balancing preparedness investments with operational efficiency – typically allocating 2-5% of procurement budgets to resilience measures yields optimal protection against disruptions.