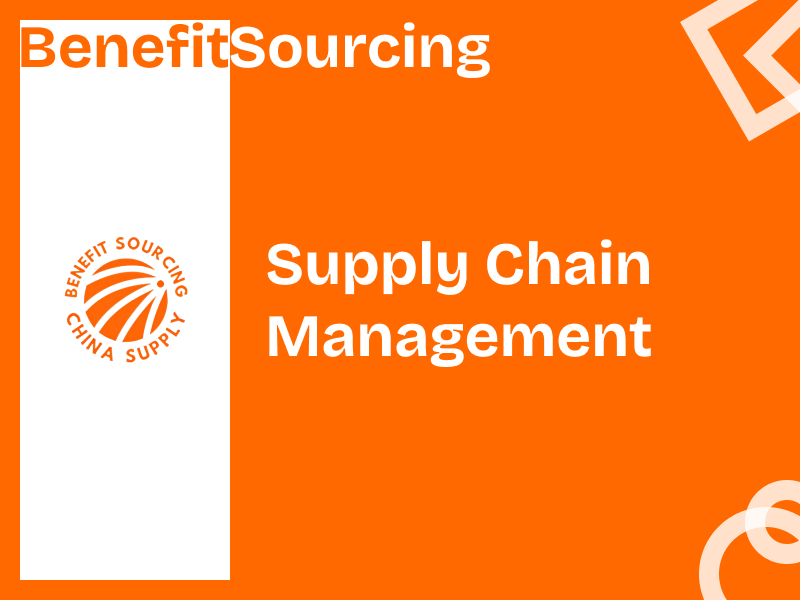
Understanding China’s Manufacturing Landscape
China’s position as the “world’s factory” stems from its unparalleled supply chain networks, competitive pricing, and diverse production capabilities. However, quality variations exist across suppliers due to differences in factory size, expertise, and compliance standards. While large manufacturers often serve global brands with ISO-certified processes, smaller factories catering to SMEs may lack formalized quality systems. This dichotomy requires buyers to implement proactive quality control (QC) strategies tailored to their specific product categories and risk tolerance.
Common Quality Challenges
-
Communication Gaps
Misinterpretations of technical specifications frequently occur due to language barriers. A “waterproof” rating might mean surviving light rain to one supplier but submersion resistance to another. Detailed documentation with visual references (e.g., annotated diagrams, comparison samples) minimizes ambiguity.
-
Diverging Standards
Chinese GB standards don’t always align with EU CE or US FCC requirements. For instance, a power bank meeting Chinese safety norms might lack essential surge protection for European markets. Buyers must explicitly specify required certifications and testing protocols.
-
MOQ Pressures
Small order quantities (<500 units) often get routed to less-established workshops where process controls may be inconsistent. Negotiating prototype approval and implementing pre-shipment inspections become critical for low-volume orders.
-
Supply Chain Complexity
Multi-tier production systems can obscure quality risks. A factory assembling electronics might source capacitors from a sub-supplier using recycled materials without the buyer’s knowledge. Supply chain mapping and component-level specifications help mitigate this.
Proactive QC Strategies
1. Technical Pack Development
Create a comprehensive document containing:
- Material specifications (e.g., stainless steel grade 304 vs. 201)
- Dimensional tolerances (±1mm vs. ±0.5mm)
- Performance testing methods (drop tests, wash cycles)
- Packaging requirements (vacuum-sealed, carton thickness)
Include photos of defect examples – a scratched surface, improper stitching, or discolored welding – to establish visual benchmarks.
2. Supplier Qualification Process
Conduct virtual factory audits via video calls focusing on:
- Machinery condition (age/maintenance records of injection molding machines)
- Workshop organization (raw material storage practices)
- QC documentation (inspection reports for previous orders)
- Social compliance (working hour records, safety equipment)
Cross-verify claims by requesting production videos and contacting existing clients through industry networks.
3. Multi-Stage Inspections
- Pre-Production: Verify raw material certificates (REACH, RoHS) and approve first article samples
- During Production: Conduct in-process checks when 20-30% of goods are completed to catch issues early
- Pre-Shipment: AQL sampling (Level II typically) for functionality, appearance, and packaging
- Loading Supervision: Ensure proper container cleanliness and stacking methods to prevent transit damage
4. Technology Integration
- Use AI-powered inspection tools like camera systems that automatically detect surface defects in textiles or ceramics
- Implement blockchain tracking for high-risk items – a Hong Kong importer reduced counterfeit pharmaceuticals by 78% using QR code tracing
- Leverage IoT sensors to monitor storage conditions during logistics (temperature/humidity for perishable goods)
Managing Defective Shipments
When quality issues surface:
- Root Cause Analysis: Distinguish between supplier negligence (wrong material substitution) and genuine misunderstandings (cultural differences in color perception)
- Negotiation Leverage: Hold final payment (typically 30% balance) until corrective actions are implemented
- Salvage Options: Consider on-site repairs (hiring local technicians), partial acceptance (70% good units), or liquidation through B2B platforms like Alibaba’s Trade Assurance
Cost-Effective Adaptation for SMEs
- Pool orders with other buyers to meet MOQs for premium factories
- Use consolidated QC services – shared inspectors covering multiple clients in industrial clusters
- Adopt graduated compliance: Basic safety certification for initial orders, progressing to full certification as sales volumes justify costs
- Utilize China’s cross-border e-commerce hubs (Guangzhou Baiyun, Yiwu Market) offering ready-to-ship stocks with pre-verified quality
Cultural Considerations
Build trust through relationship management:
- Schedule video calls during Chinese working hours (GMT+8)
- Acknowledge festivals like Lunar New Year in supplier communications
- Provide constructive feedback using indirect language – instead of “your quality is poor,” suggest “let’s work together to achieve higher standards”
Regulatory Updates
Stay informed about evolving standards:
- 2023 revisions to China’s Export Product Quality Law
- Expanding CBAM (Carbon Border Adjustment Mechanism) requirements affecting EU-bound goods
- U.S. Customs’ increased scrutiny on forced labor compliance (Xinjiang-related imports)
By implementing these tailored practices, small international buyers can systematically reduce quality risks while maintaining cost efficiency. Regular supplier scorecard reviews (delivery, defect rates, responsiveness) and staying updated on China’s manufacturing innovations (automated QC systems, green production initiatives) further enhance long-term sourcing success.