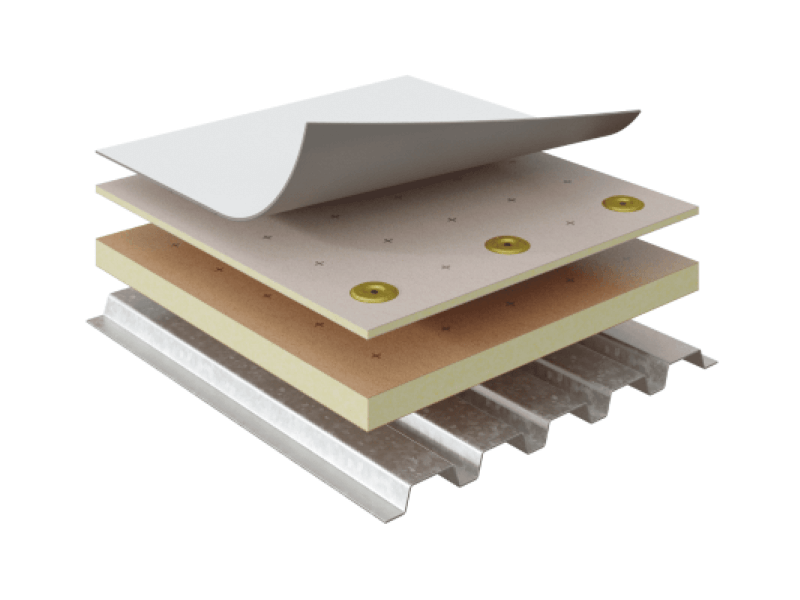
What Is an Induction Welded Roofing System?
An induction welded roofing system is an innovative technology that uses electromagnetic induction to bond TPO or PVC membranes to the roof deck or insulation without penetrating the membrane. This method employs specialized plates coated with the same material as the membrane, which are welded to the membrane’s underside using a high-frequency induction tool. By combining mechanical anchoring with molecular-level bonding, it creates a weather-tight seal that surpasses traditional fastening methods in durability and performance.
How Does Induction Welding Work?
The process integrates four core technical stages:
- Plate Preparation & Placement
Specialized plates (e.g., RhinoBond or InvisiWeld) coated with TPO/PVC are anchored to the roof deck or insulation layer using mechanical fasteners. These plates contain ferromagnetic particles that respond to electromagnetic fields.
- Electromagnetic Induction Heating
A portable induction tool generates high-frequency electrical currents, creating an alternating magnetic field. This field heats the ferromagnetic particles in the plates, raising their temperature to 200–250°C, which melts the membrane’s base layer.
- Molecular-Level Bonding
As the membrane melts, it fuses with the coated plate, forming a homogeneous bond at the molecular level. This process creates a seamless connection without penetrating the membrane, eliminating potential leak points.
- Seam Completion & Quality Control
After welding, the seam is inspected for uniformity using non-destructive testing (e.g., vacuum boxes or spark testing) to ensure watertight integrity.
Core Technical Advantages
- Superior Bond Strength
Induction welding creates bonds 30% stronger than traditional heat welding, with tensile strengths exceeding 500 N/50mm, making it ideal for high-wind zones (up to 200+ mph wind resistance).
- Non-Penetrative Waterproofing
By avoiding membrane punctures, the system eliminates 90% of common leak sources from fastener holes, reducing maintenance costs by 40% over a 20-year lifecycle.
- Installation Efficiency
Welding speeds of 12–18 linear meters per minute allow large areas (e.g., 5,000 m²) to be installed in 3–5 days, 50% faster than conventional mechanical systems.
- Environmental Sustainability
- Zero VOC emissions during installation
- 50% lower energy consumption than traditional heat welding
- Recyclable membrane-plate assemblies (meets LEED v4.1 material reuse credits)
- Reduced Membrane Flutter
The uniform bonding reduces thermal expansion-induced movement, extending membrane life by 15–20% compared to loosely fastened systems.
Key Considerations for Implementation
System Compatibility
- TPO plates must pair with TPO membranes; PVC plates with PVC membranes
- Metal decks require anti-corrosion treated plates (e.g., zinc-coated fasteners)
- Induction tools need monthly calibration to maintain precise temperature control (±5°C). Installers must complete certified training (e.g., NRCA induction welding courses) to ensure consistent weld quality.
Surface Preparation
- Membrane and plate surfaces must be free of dust, oil, or moisture (surface cleanliness affects bond strength by 25–30%)
- Rough substrates require a primer layer to ensure even heat distribution
Applications & Ideal Scenarios
- High-Wind Coastal Projects
Example: Oceanfront resorts in Florida or China’s southeastern coast, where systems must withstand Category 5 hurricane forces (157+ mph winds).
- Sensitive Healthcare Facilities
Hospitals and laboratories benefit from zero VOC emissions during installation, maintaining air quality standards (e.g., ISO 14644-1 Class 8 cleanrooms).
- Large-Scale Commercial Roofs
Logistics hubs and airports (e.g., Amazon fulfillment centers) require rapid installation of 10,000+ m² roofs without disrupting operations.
- Complex Architectural Designs
Curved roofs or domes (e.g., museums, convention centers) where induction welding adapts to irregular shapes without compromising waterproofing.
- Retrofit Projects
Overlaying existing single-ply membranes (e.g., EPDM to TPO conversion) without tear-off, saving 30–40% on demolition costs.
The induction welded roofing system represents a paradigm shift in commercial roofing, combining mechanical robustness with eco-friendly innovation. Its ability to deliver non-penetrative, high-wind-resistant installations with minimal environmental impact makes it indispensable for modern projects that demand both performance and sustainability. As urban construction continues to prioritize energy efficiency and long-term durability, induction welding is set to become the gold standard for high-performance roofing systems worldwide.